Diesel Pumps – Diesel Transfer Pumps – How They Work …………
Most Diesel Transfer Pumps are Rotary Vane Pumps….
A rotary vane pump is a positive-displacement pump that consists of vanes mounted to a rotor that rotates inside of a cavity. In some cases these vanes can be variable length and/or tensioned to maintain contact with the walls as the pump rotates. It was invented by Charles C. Barnes of Sackville, New Brunswick who patented it on June 16, 1874.
Types
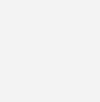
The simplest vane pump is a circular rotor rotating inside of a larger circular cavity. The centers of these two circles are offset, causing eccentricity. Vanes are allowed to slide into and out of the rotor and seal on all edges, creating vane chambers that do the pumping work. On the intake side of the diesel pump, the vane chambers are increasing in volume. These increasing volume vane chambers are filled with fluid forced in by the inlet pressure. Inlet pressure is actually the pressure from the system being pumped, often just the atmosphere. On the discharge side of the pump, the vane chambers are decreasing in volume, forcing fluid out of the diesel pump. The action of the vane drives out the same volume of fluid with each rotation. Multistage rotary vane vacuum pumps can attain pressures as low as 10−3 mbar (0.1 Pa).
Uses
Common uses of vane pumps include high pressure hydraulic pumps and automotive uses including, supercharging, power steering and automatic transmission pumps. Pumps for mid-range pressures include applications such as carbonators for fountain soft drink dispensers and espresso coffee machines. They are also often used as vacuum pumps for providing braking assistance in large trucks and diesel powered passenger cars (whose engines do not generate intake vacuum) through a braking booster, and in most light aircraft to drive gyroscopic flight instruments, the attitude indicator and heading indicator. Furthermore, vane pumps can be used in low-pressure gas applications such as secondary air injection for auto exhaust emission control, and in vacuum applications including evacuating refrigerant lines in air conditioners, and laboratory freeze dryers, diesel transfer pump, extensively in semiconductor low pressure chemical vapor deposition systems, and vacuum experiments in physics. In this application the pumped gas and the oil are mixed within the pump, but must be separated externally. Therefore the inlet and the outlet have a large chamber–maybe with swirl–where the oil drops fall out of the gas. The inlet has a venetian blind cooled by the room air (the pump is usually 40 K hotter) to condense cracked pumping oil and water, and let it drop back into the inlet. It eventually exits through the outlet.
Variable Displacement Vane Pumps
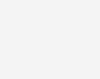
One of the major advantages of the vane pump is that the design readily lends itself to become a variable displacement pump, rather than a fixed displacement pump such as a spur-gear (X-X) or a gerotor (I-X) pump. The centerline distance from the rotor to the eccentric ring is used to determine the pump’s displacement. By allowing the eccentric ring to pivot or translate relative to the rotor, the displacement can be varied. It is even possible for a vane pump to pump in reverse if the eccentric ring moves far enough. However, performance cannot be optimized to pump in both directions.
Vane Pump Overview
While vane pumps can handle moderate viscosity liquids, they excel at handling low viscosity liquids such as LP gas (propane), ammonia, solvents, alcohol, fuel oils, diesel, gasoline, and refrigerants. Vane pumps have no internal metal-to-metal contact and self-compensate for wear, enabling them to maintain peak performance on these non-lubricating liquids. Though efficiency drops quickly, they can be used up to 500 cPs / 2,300 SSU.
Vane pumps are available in a number of vane configurations including sliding vane (left), flexible vane, swinging vane, rolling vane, and external vane. Vane pumps are noted for their dry priming, ease of maintenance, and good suction characteristics over the life of the pump. Moreover, vanes can usually handle fluid temperatures from -32°C / -25°F to 260°C / 500°F and differential pressures to 15 BAR / 200 PSI (higher for hydraulic vane pumps).
Each type of vane diesel pump offers unique advantages. For example, external vane pumps can handle large solids. Flexible vane pumps, on the other hand, can only handle small solids but create good vacuum. Sliding vane diesel pumps can run dry for short periods of time and handle small amounts of vapor.
How Vane Pumps Work
Despite the different configurations, most vane pumps operate under the same general principle described below.
1. A slotted rotor is eccentrically supported in a cycloidal cam. The rotor is located close to the wall of the cam so a crescent-shaped cavity is formed. The rotor is sealed into the cam by two sideplates. Vanes or blades fit within the slots of the impeller. As the rotor rotates (yellow arrow) and fluid enters the pump, centrifugal force, hydraulic pressure, and/or pushrods push the vanes to the walls of the housing. The tight seal among the vanes, rotor, cam, and sideplate is the key to the good suction characteristics common to the vane pumping principle.
2. The housing and cam force fluid into the pumping chamber through holes in the cam (small red arrow on the bottom of the pump). Fluid enters the pockets created by the vanes, rotor, cam, and sideplate.
3. As the rotor continues around, the vanes sweep the fluid to the opposite side of the crescent where it is squeezed through discharge holes of the cam as the vane approaches the point of the crescent (small red arrow on the side of the pump). Fluid then exits the discharge port.
Advantages
| Disadvantages
|
Applications
- Aerosol and Propellants
- Aviation Service – Fuel Transfer, Deicing
- Auto Industry – Fuels, Lubes, Refrigeration Coolants
- Bulk Transfer of LPG and NH3
- LPG Cylinder Filling
- Alcohols
- Refrigeration – Freons, Ammonia
- Solvents
- Aqueous solutions
At Atkinson Equipment Ltd and Fueldump we supply the best in Diesel Pumps and Diesel transfer pumps on the market at the moment. Most of the diesel transfer pumps we supply are Swiss/German made and come with a long manufacturers warranty. Please see our Diesel Pump Section on our website at www.fueldump.co.uk